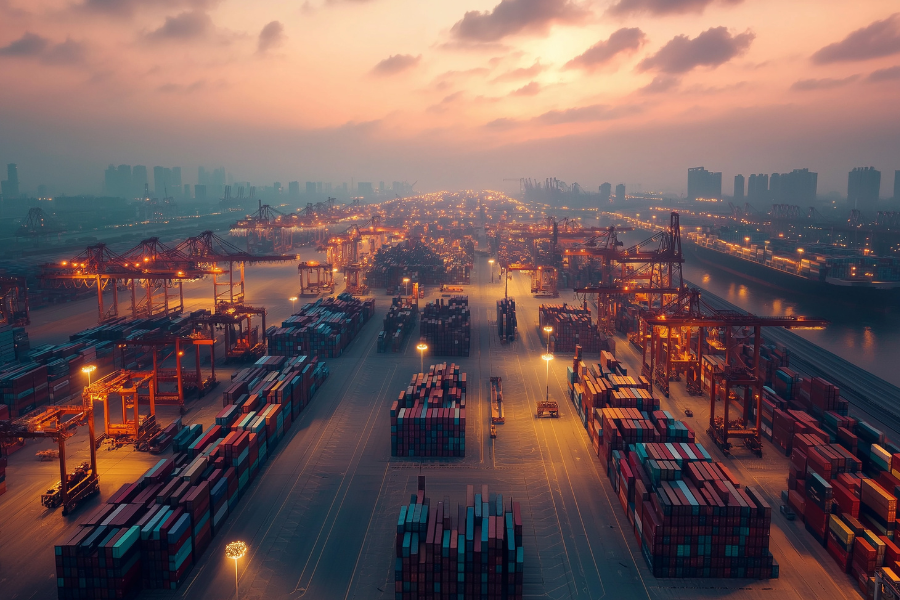
Short-Term Pain or Long-Term Innovation?
With the recent expansion of tariffs on imported steel and Canadian lumber, the design and construction industry is again bracing for increased costs and potential supply chain disruptions. The big question is whether this will be short-term pain—or if it could catalyze innovation in how we design and build.
To understand where we might be headed, we can look back at the 25% steel and aluminum tariffs introduced in 2018. While we might model how similar policies could impact costs in 2025 through 2027, the situation is complicated. The onset of the COVID-19 pandemic shortly after the tariffs were enacted caused unprecedented global supply chain disruptions. The resulting bottlenecks make it challenging to isolate the effects of the tariffs alone.
One clear example was the sudden unavailability of steel bar joists—a critical component in floor and roof assemblies. As demand for new construction surged during the post-pandemic economic reopening, bar joists became almost impossible to source. Imported steel became more expensive, and domestic production couldn’t quickly fill the gap. On top of that, there are very few U.S. bar joist manufacturers. What used to be a 6- to 8-week lead time ballooned to 30 to 50 weeks.
As a result, our office had to redesign nearly every project, substituting steel beam and metal deck assemblies in place of bar joists—a significantly more expensive approach. This reactionary adaptation will likely repeat itself in the short term as tariffs continue to affect not just steel but also Canadian softwood lumber, which now faces duties as high as 39.5%. These added costs are already impacting budgets and forcing design choices that compromise performance and aesthetics.
These tariffs could create serious headwinds in high-growth metro areas where housing demand and affordability are already strained. Developers will push forward with projects already funded, but many may pause new developments until costs stabilize. Only so much of the cost can be passed on to buyers before the math no longer works. As risk increases and margins shrink, those who can innovate will emerge as leaders in what may become a very different landscape.
Perhaps mass timber—specifically Cross-Laminated Timber (CLT) will become a more promising construction alternative in the U.S.. While steel, concrete, and block remain standard in the U.S., Europe has used CLT for mid- and high-rise construction since the 1990s. Traditional materials are costlier in those markets, making CLT—along with its sustainability advantages—a more competitive and desirable option. In the U.S., we’ve seen a growing number of CLT manufacturing facilities open, but a steel-framed building is still generally cheaper—for now.
Still, if there’s one lesson from the pandemic, it’s that our profession can pivot quickly when needed. Shortly following the pandemic, we were forced to rethink how we design buildings almost overnight, and we did. The truth is that humans, as well as Architects, are remarkably resilient. We find new ways forward when pushed by economic forces or global challenges. Perhaps, as we have seen in the past, these tariffs and their impact on the design and construction industry will be the spark that forces innovation out of necessity.